Hongwo : Expertly Engineered FRP Platforms for the Chemical Industry
Hengshui Hongwo Technology Co., Ltd. specializes in crafting Fiberglass Reinforced Plastic (FRP) platforms for chemical plants, skillfully blending technical know-how with practical design. These platforms are engineered to meet the challenging conditions of chemical environments, with a strong focus on worker safety and environmental compliance. Their integration into the chemical industry is marked by unmatched durability, safety, and operational efficiency.
FRP, renowned for its excellent corrosion resistance, is the chosen material for these platforms, ensuring both longevity and reduced maintenance. The heat resistance of FRP gratings, a vital feature, depends on the resin type used and typically withstands temperatures up to 150°C (300°F). This demonstrates the company’s commitment to high-quality solutions adaptable to a variety of chemical processes.
Designed to operate over a broad temperature spectrum, these platforms cater to diverse processing needs:
- Low-Temperature Processes: Optimal for -50°C to 5°C, making them ideal for gas separation and other low-temperature tasks.
- Ambient Temperature Processes: Efficient between 15°C and 35°C, they are suited for everyday operations like mixing and storage.
- High-Temperature Processes: Robustly built to endure 100°C to over 150°C, these platforms are specifically designed for high-heat thermal chemical reactions.
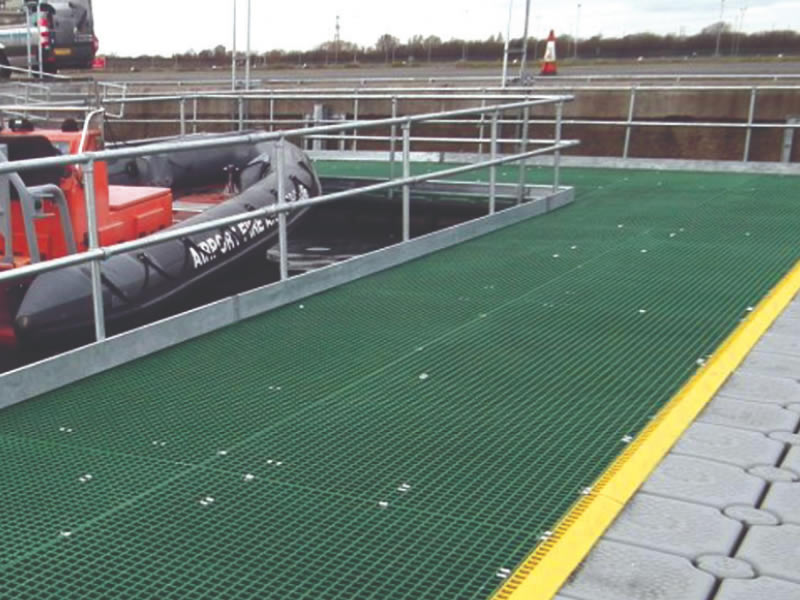


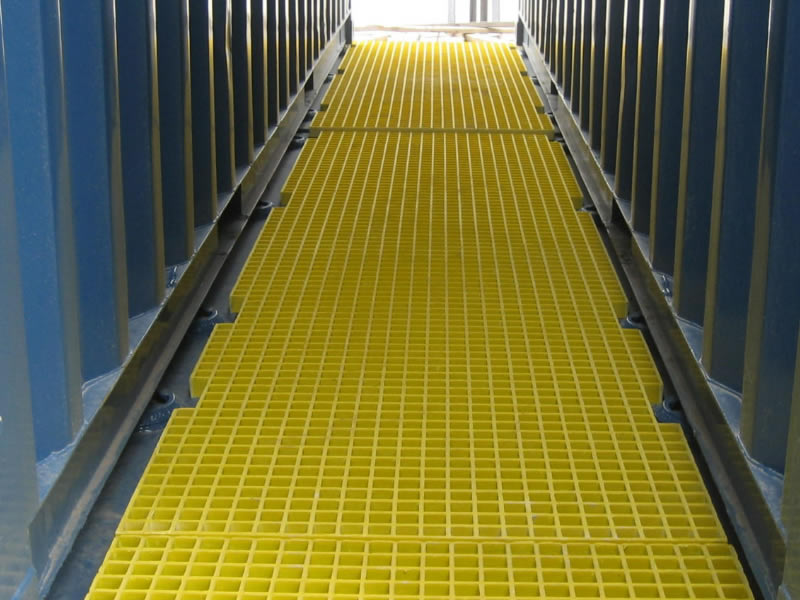


Initial Preparation Work for FRP Grating Platform:
- Material Selection:
Opt for FRP grating materials with high resistance to chemicals, heat, and mechanical stress.
Ensure compatibility with industry standards, such as ASTM. - Load Calculations:
Estimate both static and dynamic loads, factoring in equipment, personnel, and environmental influences.
Account for live load, dead load, and impact load. - Dimensioning:
Specify platform size, height, and span dimensions.
Consider environmental impacts like expansion and contraction. - Safety Features:
Incorporate railings, non-slip surfaces, and toe boards for safety.
Adhere to OSHA and other relevant safety standards. - Drainage and Ventilation:
Design for effective drainage to prevent chemical spills.
Include ventilation planning for potential gas emissions. - CAD Modeling:
Develop detailed CAD models of the platform, including supports, grating, fasteners, and accessories.
Main Product Specifications
Small-Hole Cross-Grid Fiberglass Grating Platform: Precision and Durability for Various Industries
- Usage: Chemical Industry, Sewage Treatment, Greening, Breeding
- Color Options: Yellow, Green, Red, Grey, Black, White
- Hole Pattern: Square, Mesh Size 33x33mm
- Thickness: 8mm
- Compressive Strength: 500 or 1000MPa
- Type: Fiberglass Grille
- Material: Fiberglass
- Available Heights: 25mm, 30mm, 38mm, 50mm
- Features: Corrosion Resistance
- Service Life: Up to 10 Years
- Packing: Bale
- Manufacturing Process: Molded Fiberglass Composite
- Model: Cross Grid
Custom-Designed FRP Grating Platforms for Small Chemical Plants: Durable and Corrosion-Resistant
- Thickness: 8mm
- Available Heights: 25mm, 30mm, 38mm, 50mm
- Color: Yellow
- Application Areas: Electric Power, Chemical Plants
- Load Bearing Capacity: 200kg
- Key Advantage: Corrosion Resistance
- Installation: Assembly Method
- Manufacturing Process: Pultruded FRP Grating
- Bolted Connections: Yes
- Compressive Strength: 1000MPa
- Intended Use: Maintenance Platforms
- Material: Fiberglass
- Customization: Available for Specific Needs and Export
Installation Phase
- Site Preparation:
Clear the area and prepare a stable foundation.
Check for underground utilities or structures. - Component Inspection:
Inspect all delivered components for defects or damage.
Verify dimensions and material specifications. - Assembly of Support Structure:
Construct the support structure according to the design specifications.
Ensure proper alignment and leveling. - Grating Installation:
Lay down the FRP grating panels.
Secure them to the support structure with appropriate fasteners, ensuring no movement. - Safety Features Installation:
Install safety railings, kick plates, and other safety features.
Ensure they are firmly attached and meet safety requirements. - Quality Assurance:
Conduct load testing to ensure the platform can handle the expected loads.
Inspect for any installation defects or issues. - Final Inspection and Handover:
Perform a final inspection to ensure all aspects meet the design specifications and safety standards.
Hand over the platform to the plant management with maintenance and safety guidelines. - Post-Installation
Training:
Train the staff on the safe use of the platform.
Provide information on load limits and safety precautions. - Maintenance Plan:
Develop a maintenance schedule for regular checks and repairs.
Include guidelines for dealing with chemical spills or environmental damage. - Documentation:
Provide detailed documentation including design drawings, material specifications, and maintenance procedures.
Each step in this process is crucial for ensuring that the FRP grating platform is safe, durable, and suitable for the harsh conditions of a chemical plant. It’s important to involve experienced engineers and adhere to all relevant industry standards throughout the design and installation process.