FRP Cable Tray Sizing: Ensuring Load Capacity
Hengshui Hongwo Technology Co., Ltd. manufactures FRP cable trays and specializes in the design and installation of various FRP cable tray projects. To ensure the proper use of Fiber Reinforced Plastic (FRP) cable trays in these projects, it is important to adhere to the following specific guidelines:
Material Selection
Choose the correct grade of FRP for the specific environment. FRP trays come in various compositions, each suitable for different conditions, such as corrosive environments, high-temperature areas, or outdoor exposure.
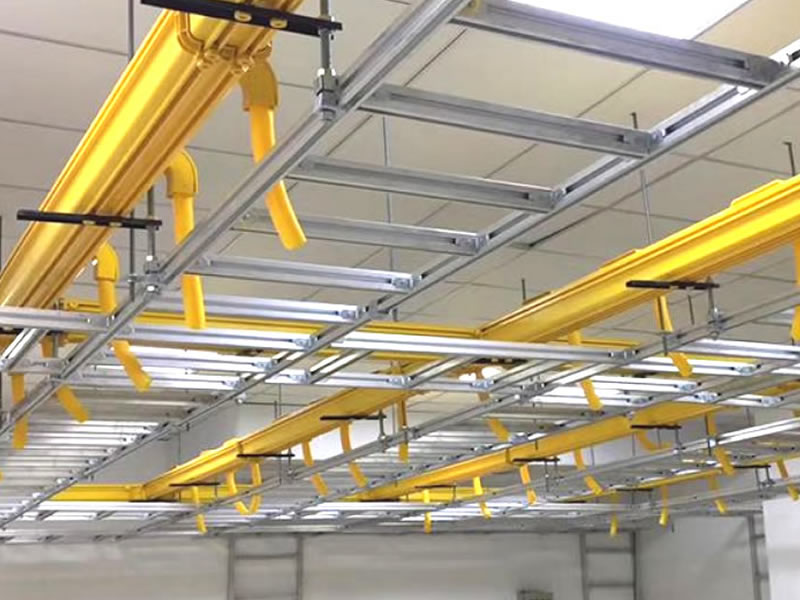
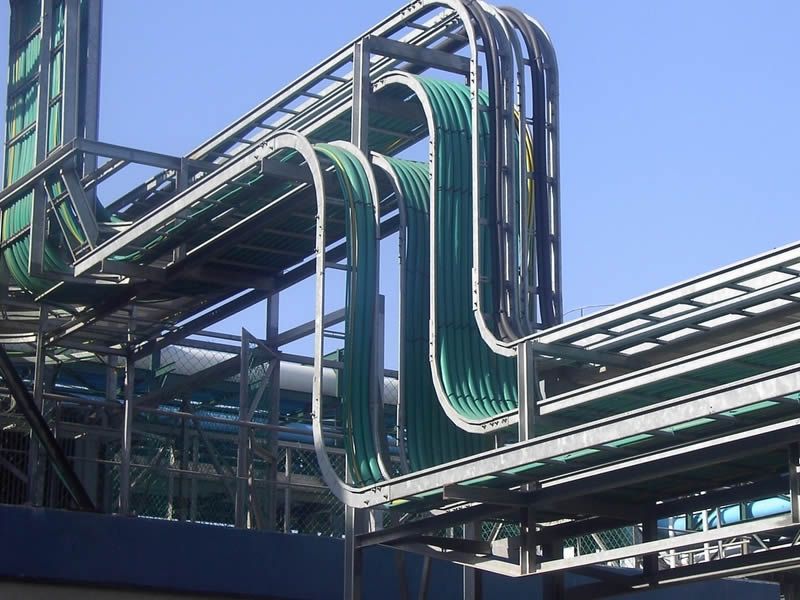
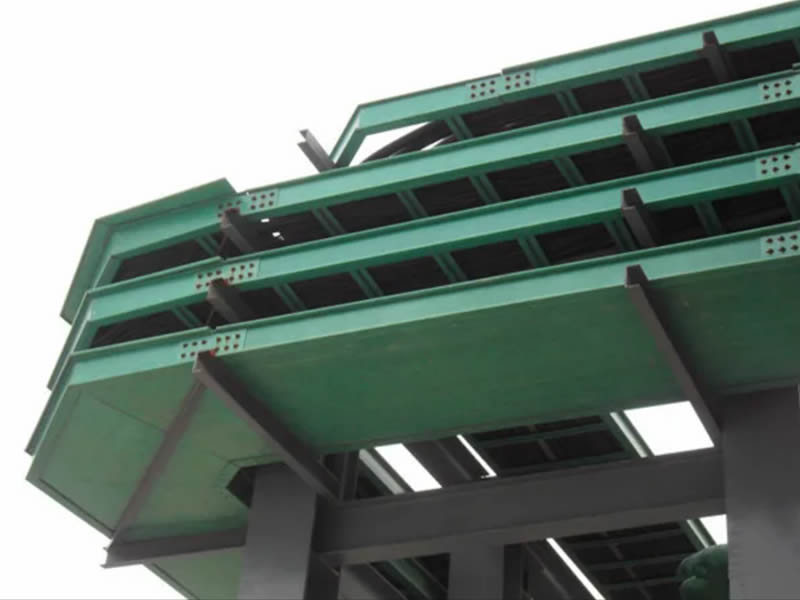
Load Capacity and Sizing
Determine the appropriate size and strength of the cable tray based on the type and number of cables it will carry. Overloading can lead to structural failure.
- Understanding Load Types: The load on cable trays can be of two types: static and dynamic. Static load refers to the weight of the cables themselves, while dynamic load accounts for additional forces such as those from wind or seismic activity. It’s crucial to consider both types when determining load capacity.
- Calculating Cable Weight: Calculate the total weight of the cables that the tray will carry. This includes the weight per unit length of each cable type and the total length of cable to be supported. The combined weight should not exceed the specified load capacity of the FRP cable tray.
- Accounting for Future Expansion: It’s wise to plan for potential future additions of cables. This foresight can prevent the need for costly upgrades or replacements if additional capacity is needed later.
- Span Length: The span length, or the distance between supports of the cable tray, plays a significant role in determining the load capacity. A shorter span can support more weight, whereas a longer span reduces the load capacity.
- Tray Width and Depth: The size of the cable tray, including its width and depth, affects its load capacity. Wider or deeper trays can generally hold more or larger cables, but this also depends on the tray design and material.
- Safety Factor: Always include a safety factor in your calculations. This is an additional percentage (commonly around 1.5 to 2 times) added to the anticipated maximum load to ensure a margin of safety.
Installation Guidelines
Installation guidelines for Fiber Reinforced Plastic (FRP) cable trays are critical for ensuring both the safety and longevity of the system. Proper installation not only supports the structural integrity of the cable trays but also ensures compliance with safety standards and regulations.
- Pre-Installation Planning: Before beginning the installation, it’s essential to have a detailed plan. This includes understanding the layout, identifying the paths for the cable trays, and ensuring that all necessary materials and tools are available. Also, check for any obstructions along the path where the trays will be installed.
- Reading Manufacturer’s Instructions: Each FRP cable tray system may have specific requirements or recommendations for installation. Always start by thoroughly reading and understanding the manufacturer’s installation guide.
- Support Structures: Ensure that the support structures for the cable trays are robust and securely anchored. The supports should be capable of handling not just the weight of the trays and cables but also any additional loads, such as those from wind or seismic activity.
- Correct Spacing of Supports: Adhere to the manufacturer’s recommendations for the spacing of supports. Incorrect spacing can lead to sagging or collapse of the cable trays.
- Level and Alignment: During installation, make sure the cable trays are level and properly aligned. Uneven or misaligned trays can compromise the system’s integrity and capacity.
- Securing the Trays: Use appropriate fasteners and connectors as specified by the manufacturer. Ensure that all connections are tight and secure to prevent movement or dislodging of the trays.
- Thermal Expansion Consideration: FRP materials can expand or contract with temperature changes. Allow for thermal expansion in the design and installation of the cable tray system. This often involves using expansion joints or leaving sufficient gaps at the joints.
- Grounding and Bonding: Even though FRP is non-conductive, consider the requirements for grounding and bonding based on the overall electrical system design to ensure safety.
- Access for Maintenance and Inspection: Install the trays in such a way that they are easily accessible for regular inspections, maintenance, and future cable additions or changes.
- Avoid Sharp Bends: When laying out the cable trays, avoid sharp bends as they can lead to cable damage. Use appropriate fittings for changes in direction, in compliance with cable manufacturer’s guidelines and electrical codes.
- Load Distribution: Distribute the cables evenly in the trays to avoid uneven loading, which can lead to structural stress and potential failure.
- Safety Compliance: Ensure that the installation complies with local building codes, safety standards, and industry best practices. This includes maintaining clearances from other systems and ensuring that the installation does not pose a hazard.
- Inspecting Before Use: Once installation is complete, inspect the entire system to ensure everything has been installed correctly and that there are no loose parts or structural issues.
Accessories and Fittings
Use compatible accessories and fittings designed for FRP cable trays. Mismatched components can lead to weak connections or corrosion issues.
Regular Inspections and Maintenance
Schedule regular inspections to check for any signs of wear, damage, or corrosion. Promptly repair or replace damaged sections.
Safety Compliance
Ensure that the installation complies with relevant safety standards and building codes. This includes clear labeling and maintaining access for inspection and maintenance.
Ventilation
Provide adequate ventilation around the cable trays, especially if the cables generate heat. This prevents overheating and degradation of the FRP material.
Fire Safety
Consider the fire-retardant properties of the FRP material, especially in areas with a high fire risk. Some FRP trays are designed with fire-resistant properties.